I started with the Xk140 block with the Xk120 head.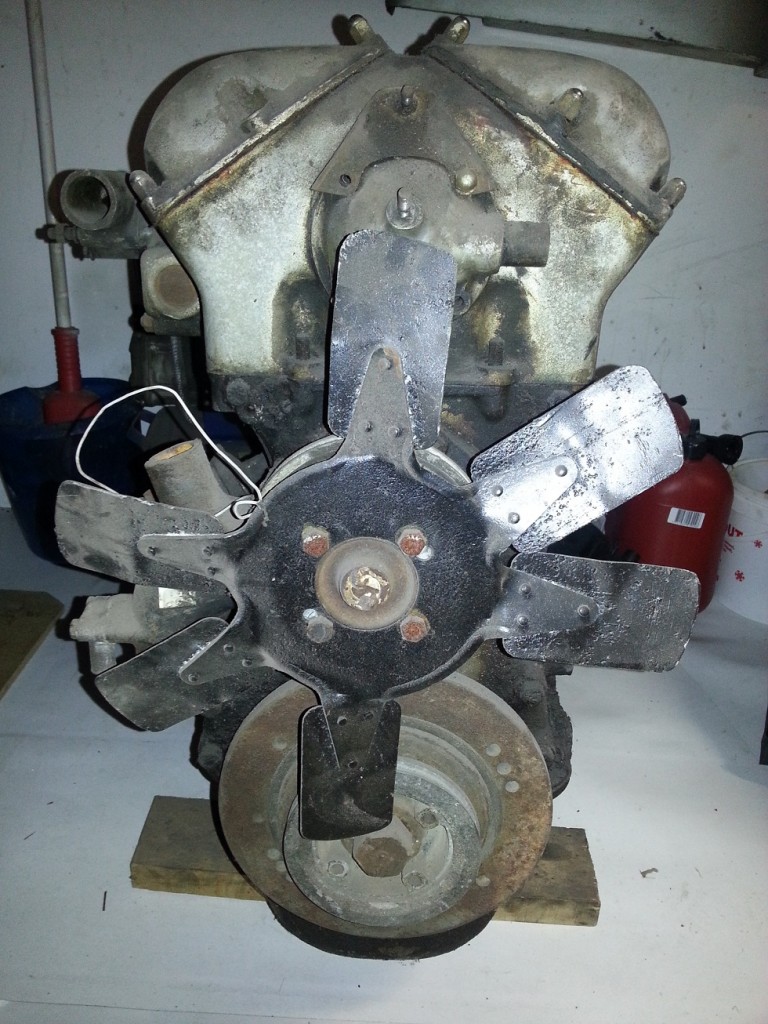
The water pump, pulley and crankshaft damper are correct and can be reused for assembly of the original XK140 engine.
The Inlet manifold on the XK140 head was damaged by corrosion, but in the mean time I found a good replacement on the internet.
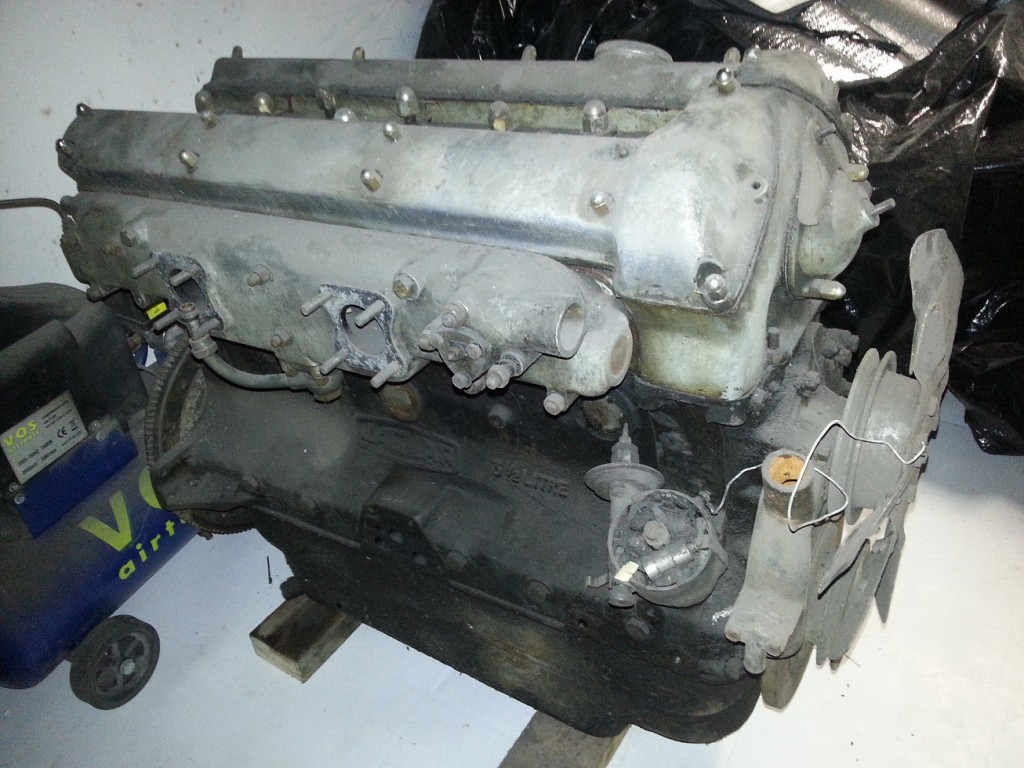
The shown fan blades are suitable for a XK120 luckily the other engine has a XK140 fan blades mounted so that one will be used instead.
Both engines where not able to turn around freely, so the 46 years of sitting still, has not been good for the overall condition. Was the engine stalled at some time, there is only one way to find out.
After removal of the oil sump the internals of the engine looked pretty normal. No broken crankshaft or broken connecting rods or other visible damage.
Remark: Label all bearing cap so they can be mounted on the exact same location and orientation. (In my case all caps where already marked with a unique id and number)
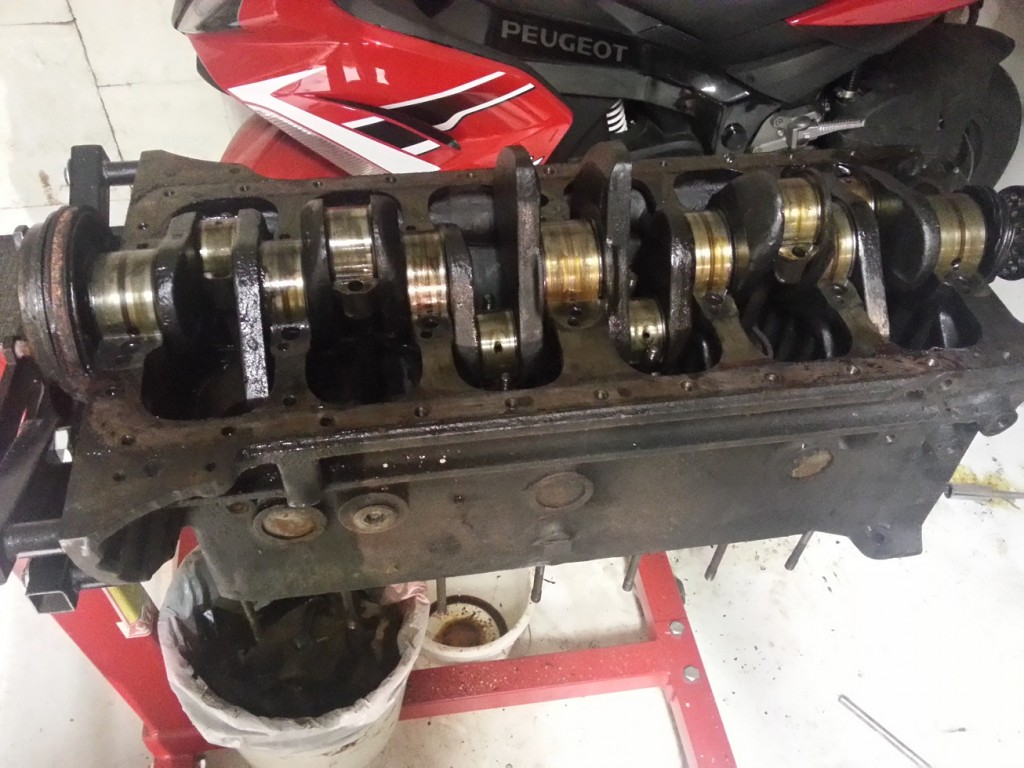
XK140 block without bearing caps
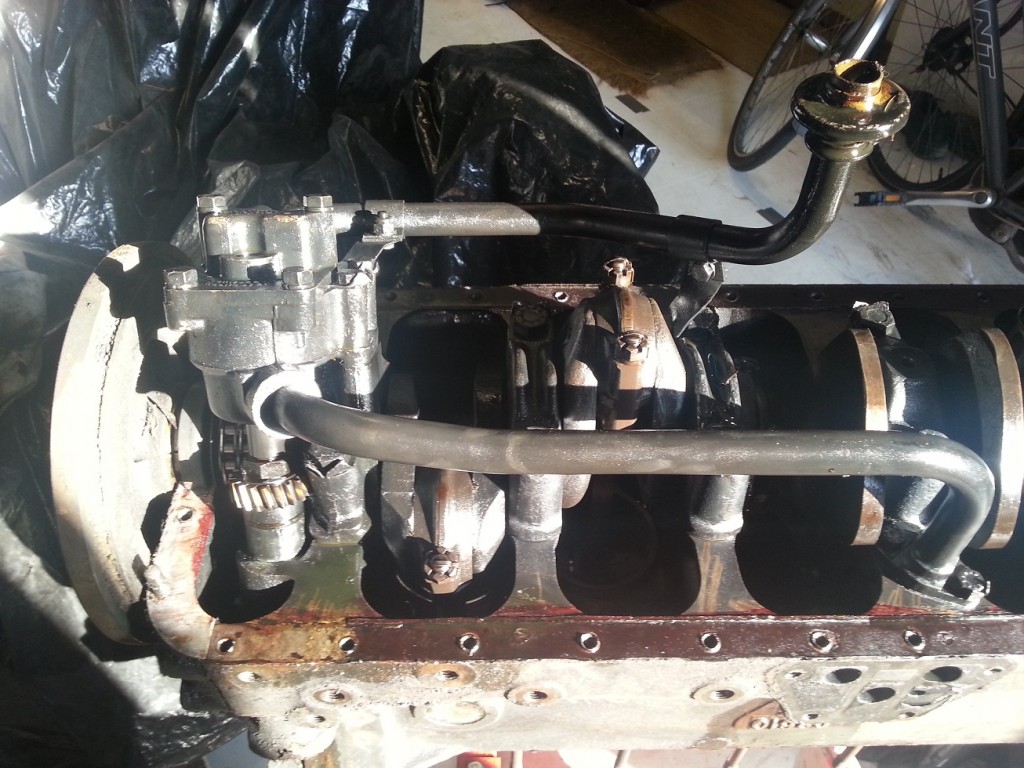
Oil pump with connection pipes
After everything is disassembled and thoroughly cleaned I started with the the removal of cylinder head. Still searching for the cause of the not freely turning engine.
When the cylinders and pistons where visible, after the head was removed, it was all clear. Two cylinders where completely filled with lime, rust and dirt. After this was removed it was visible that one cylinder was badly damaged.
After measuring the diameter I found out that all cylinders where still standard with about 6/1000″ of wear.
Most probably the cylinder has to be drilled two sizes bigger +0.020 due to wear and corrosion damage.
Although the bearing caps has a unique id and number (stamped in the block and bearing caps) someone also made some unnecessary identification with a center punch (one has been marked wrongly!).
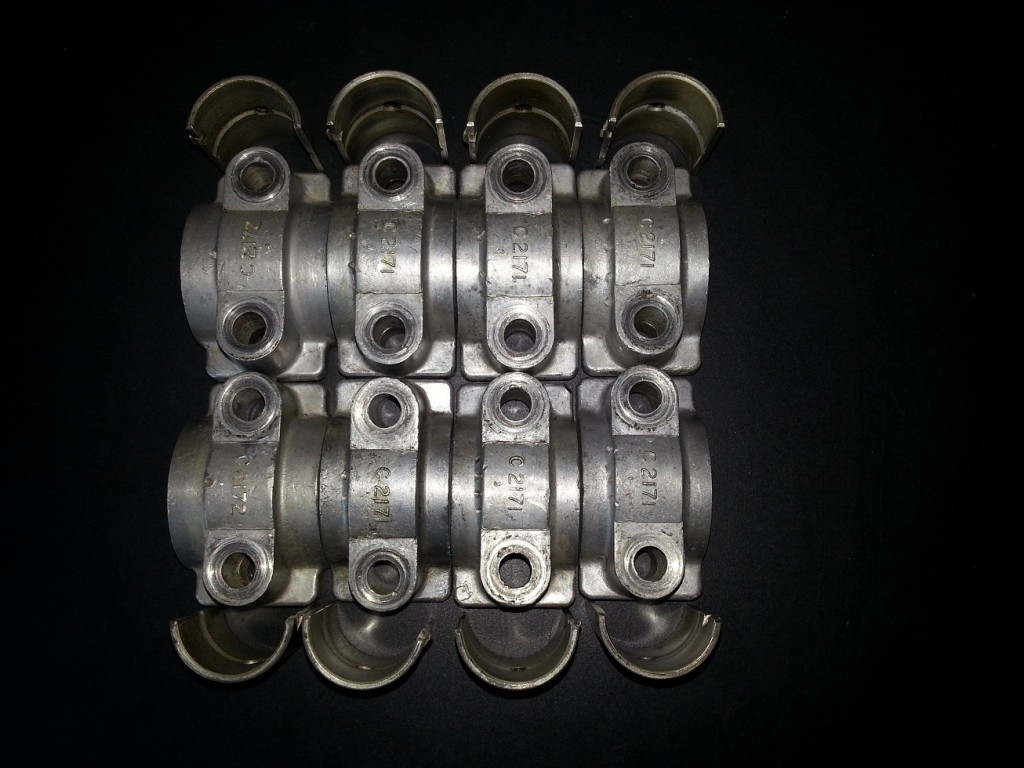
Cleaned cam shaft bearing caps